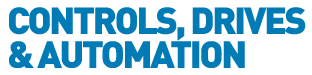
![]() |
Charlotte Stonestreet
Managing Editor |
3D printing: Which process is suitable for which application?
14 February 2019
First used in rapid prototyping, today 3D printingis increasingly used in additive processes that enable volume production of plastic and metal parts. It is also used to manufacture parts that are too complex for traditional injection moulding. The trend is towards modular and scalable manufacturing solutions tailored to a particular application. This article provides an overview of processes and trends
A key benefit of 3D printing is that it can produce metal or plastic parts lighter than those produced by conventional manufacturing processes. This is important in industries with a strong future, such as automotive, aerospace and consumer electronics. For instance, the cost of putting a satellite into geostationary orbit can be up to USD 20,000 (EUR 16,000) per kilogram. The potential cost savings from weight reduction and the possibility of producing highly complex parts quickly are fuelling a boom in 3D printing in industrial manufacturing. It is therefore not surprising that global turnover on 3D printers and accessories, materials, software and services rose from USD 529 million in 2003 to USD 3.07 billion in 2013. Annual growth is estimated at 45.7%, and another study has predicted a market volume of around USD 17.2 million in 2020.
With the range of 3D printers, technologies and materials growing steadily, users are faced with the question of which solution to choose. It is advisable to start with the finished part and its intended purpose, and to determine the process, software, material and printer on that basis. What properties should the part have? Where and how will it be used? Will it be used as a ‘lost mould’ as a step in a production chain, will it be refined and finished or installed as it is, or is the plan to scale up to series production? Future-proofing is another consideration: will the printer be able to deal with changing requirements? Successful 3D printing depends on detailed planning.
SLA process
In the stereolithography (SLA) process, liquid plastic materials (photopolymers) are cured by UV radiation on a build platform. Each part is built up with layers of resin in a process also known as photopolymerisation (PP). The parts are produced directly from 3D CAD data without tools. During the process, the build platform is submerged in the photopolymer, and the UV source is usually a laser. When a part is finished, it is cleaned in a solvent to remove any resin. The part is then cured in a UV oven.
SLA technology can be used where shape, fit and assembly are crucial. Using SLA for high-precision parts saves time, particularly when a number of prototypes are required or a single model needs to be produced quickly. SLA covers more applications than any other additive manufacturing process, including rapid manufacturing applications for high-precision and long-lifecycle prototypes. The tolerances of an SLA component are typically less than 0.05mm, and it offers the smoothest surface of all additive manufacturing processes.
SLS technology
The selective laser sintering (SLS) process builds up a thermoplastic workpiece layer by layer. The application of laser radiation then produces complex three-dimensional forms. It is possible to produce workpieces that could not be made by conventional methods. Complete assemblies can be printed as one part, which cuts costs and improves functionality and operational safety. The thermoplastic powder is applied to a build platform and the layers are sintered into the powder bed. The build platform is then lowered slightly and a new layer applied. A key benefit is that there is no need for support structures. Users can also choose from various thermoplastics which differ in rigidity, robustness and heat-resistance.
MJP
The MultiJet printing (MJP) process produces precision plastic parts for prototypes, form and fit models or rapidly produced alternatives to tools. MJP printers from 3D systems can print rigid or flexible parts with ABS-like plastics and real elastomers. It is even possible to produce compound materials with custom-made mechanical properties, and to print complex parts with several materials. One of the key features of MJP is exceptional resolution, with a layer thickness of just 12 micrometres. Surfaces are smooth and have a level of precision almost equal to that of SLA printers. With MJP printers it is also possible to print support structures from a wax which can easily be melted out of a printed part in an oven.
Digital moulding & DLP
Digital moulding is an alternative to injection moulding. 3D Systems’ Figure 4 technology is used in this context. Digital moulding is scalable and can be integrated in automated production lines. It is possible to manufacture large- and small-volume series and to switch to different parts quickly during production. This allows manufacturers to repeat a design quickly.
Figure 4 technology comprises an arrangement of extremely fast membrane-micro digital light printing (DLP) printers. This allows the efficient use of parallel manufacturing processes. Each of printer makes physical objects at an extremely high speed. Depending on the shape and material, a 3D object can be drawn out of a 2D base at a millimetre per minute. Robot arms guide the parts through each step, and parts can be manufactured continuously.
Unlike other 3D printing processes, which use photopolymers, Figure 4 offers the option of manufacturing parts from hybrid materials (multi-modal polymerisation). These are robust, long lasting and biocompatible, with high temperature resistance and elastomeric characteristics. This enables application in long-lasting consumables, the automotive industry, aerospace, healthcare and other areas.
DMP
Direct metal printing (DMP) is an additive manufacturing method that can make metal parts which are more robust, lighter, longer-lasting and give better performance than milled or cast metal parts. The consolidated manufacturing of a single highly complex part reduces costs, and means less installation work, fewer errors and less waste. Having fewer parts also simplifies logistics and supply chain management, as well as reducing product development and production time.
More manufacturers are using metal printers for series production, and the need for scalable, modular solutions is growing. A recently launched example of this is the fully scalable DMP Factory 500, a scalable manufacturing system developed joint project by 3D Systems and GF Machining Solutions. By utilising this system manufacturers will be able to increase their productivity, the quality of their parts and the safety of their processes. The build space of the printer module (500 x 500 x 500 mm) allows the production of large components as well as the simultaneous production of several pieces. An integrated powder management system ensures that the printed parts are uniform and of reproducible quality. Printing in an atmosphere with oxygen at less than 25 ppm allows the highest material quality as well as minimum use of protective gas, reducing TCO. The DMP Factory 500 also requires minimum user involvement. The whole solution is designed for uninterrupted operation and can be configured individually to meet customer needs.
Key Points
- Cost savings from weight reduction and ability to produce highly complex parts quickly fuelling 3D printing boom in industrial manufacturing
- MJP produces precision plastic parts for prototypes, form and fit models or rapidly produced alternatives to tools
- More manufacturers are using metal printers for series production, and the need for scalable, modular solutions is growing
- No related articles listed